Articles & Publications
Atlanta Motor Speedway races back to operation after Tropical Storm Cindy
Facility condition assessments, especially after a wind or seismic event, can be very challenging, educational, and exciting work for a structural engineer. This work gets you away from your comfort zone, the office, and into the field where you have to rely on your practical and experienced judgment to identify the signs of distress and the probable causes. Structural engineers spend a great deal of time designing for wind and seismic events, however, it is a rare opportunity to see and understand firsthand the outcome of such an event.
Innovative Engineering Inc. (IEI) had such an opportunity this past year working on a high profile project for the Atlanta Motor Speedway (AMS) after a tornado struck the facility. After overcoming the inertia of getting employees out of the office, no one complained about the short notice, long hot days, and weekend work. After the first day, everyone – registered engineers and interns alike – thought this work was quite intriguing.
The AMS, located 30 miles south of Atlanta near Hampton, Ga., is one of only three remaining original superspeedways in the country. The 870-acre complex consists of a 1.54-mile oval track, infield garages, media centers, and camping facilities. Grandstands provide seating for 124,000 spectators, and there are 137 luxury suites. At the edge of the grandstands is a nine-story luxury condominium and office building, Tara Place. There are also support buildings outside the grandstands for ticket and souvenir sales, catering, camping, and parking.
Spawned from the remains of Tropical Storm Cindy that struck Georgia on Wednesday, July 6, 2005, a tornado rated an F2 on the Fujita scale touched-down at the speedway. (The Fujita Scale is used to rate the intensity of a tornado by examining the damage caused by the tornado after it has passed over a man-made structure. The rating extends from the lowest of F0 to the highest of F5.) At this time, little did anyone know that this storm was only the beginning of what would become known as the most active hurricane season in the last century. Interestingly the bowl shape of the speedway actually helped the tornado to form. The tornado remained on the ground for approximately four miles, generated 150-mph winds, and grew to 1/2 mile wide, according the National Weather Service.
The tornado caused heavy structural damage to parts of the grandstands, luxury suites, condominiums, corporate offices, and the infield area at AMS. Roofs and facades were torn off buildings, many windows were broken, a 50- foot scoreboard tower was knocked down, and many other signs and lamp posts were damaged. The track was covered in heavy debris. Initially, officials estimated the complex suffered as much as $40 million dollars in damage.
AMS employees wasted no time in putting its wheels in motion by contacting several engineers and contractors that they and the owners (Speedway Motorsports Inc.) had worked with previously. The team was determined to have repairs made before the start of one of the facility’s largest events – the Bass Pro Shops MBNA 500 – scheduled for October 28-30, less than four months away.However, because of possible safety concerns with entering buildings, a structural integrity analysis was requested by the county prior to allowing building occupants and contractors to enter the facility for repairs and reconstruction efforts. IEI was asked by Savant Engineering, LLC to perform a structural integrity evaluation of 41 buildings as part of the initial Facility Condition Assessment. A kick-off meeting was held with the owner, other engineers, and contractors on Friday, July 8 – only two days after the tornado hit the speedway.
Logistics
As with any successful project, planning was imperative. IEI’s first order of business was to perform a cursory walk through of the facility to identify the types and extents of damage, as well as potentially hazardous conditions that teams would be encountering. Next, the company’s standard condition assessment checklist was modified for this project. (The checklist used is similar to that published by The Applied Technology Council in its Field Manual ATC 45. This manual is a good guide for performing post wind damage assessments, and its checklist is a helpful starting point.) To help organize the project, a site plan was needed to identify the buildings and plan how the team would complete the assessments. Since a site plan was not available, one was downloaded from Google Earth. From this Internet site, the team was able to get a very good satellite photograph of the facility that included all of the 41 buildings needing to be assessed. Even though each building had a functional name, IEI engineers numbered them on the satellite photo so there would be no confusion both in the field and in the reports. Professional staff was then organized into two-person teams consisting of one registered engineer and one engineering intern. Each team was outfitted with the following equipment:
- air-conditioned vehicle;
- stocked cooler;
- cell phone;
- folding ladder;
- clip board;
- digital camera with date stamp;
- flashlight, preferably 1 million candle power;
- tool belt or surveyor’s field vest to carry equipment; and
- optional equipment such as a mason’s hammer, a tape measure, calipers, a compass, and a T-handle soil probe.
Prior to deploying teams to the site, IEI verified that the electricity and natural gas were turned off in the buildings to be assessed. Also, the teams verified that a representative from the facility would be available full time to ensure access to the buildings. Eating establishments and functional toilet facilities also were identified.
Safety meeting
The team participated in a safety meeting before conducting the first assessment. This meeting was similar to those conducted by the construction industry. The following topics were discussed:
Buddy system – Because of the quantity of equipment carried and the potential hazards encountered, two people can work much more efficiently and safely than two individuals working alone.
Communication – Assessors were told that communication by cell phone was preferred since emergency help cannot be called from some walkie-talkies.
Protective clothing – Proper attire was announced to include hard-soled shoes, long pants, and hard hats.
Physical well-being – Team members were encouraged to stay hydrated while physically exerting themselves in the heat, and to take advantage of the air-conditioned vehicles.
Specific hazards – Aside from first responders, structural engineers are typically the first to enter a building being assessed. Safety is of the utmost importance. Teams were reminded that walls may have been blown out, and it is likely that unprotected building edges are exposed. By using a tool belt or a surveyor’s vest to carry equipment, inspection team members learned they could keep their hands free to prevent falling. Also, they were told to be aware of what was on the floor. For example, loose or displaced roofing and floor covering could conceal a hole in the deck or there could be loose pieces of lumber with exposed nails.Teams were encouraged to refrain from walking and taking notes at the same time. And, as on any construction site, they were told to never step backwards and to be aware of potential falling debris and hazardous materials.
Exterior observations – Assessors were instructed to walk the perimeter of a building and to observe the roof before entering to help identify what types of damage to expect and also to determine what portions of the building are unsafe to enter. They were told to keep in mind that if an area of a building is structurally unsafe to enter, it will likely need to be demolished. Therefore, in lieu of jeopardizing personal safety, take some notes and photographs to document why a portion of the building was not entered.
Seek shelter – Subsequent storms are common, especially after a wind event. Therefore, assessors were told to identify a safe location where shelter could be sought in the event that a storm occurred while performing a condition assessment. Also, they were reminded to vacate potentially damaged buildings in the event of high winds or electrical storms.
The assessment
After a cursory review of the damage on Friday afternoon, IEI modified the condition assessment checklist for this particular project. The use of a checklist prompts assessors to examine visually and describe all vertical load carrying structural systems, as well as the building’s lateral system and foundation. By focusing on the structural elements, the structural engineer’s job can be simplified. Often times a building appears more heavily damaged than it actually is from a structural standpoint. One example is the Weaver Skybox building shown in the photographs on pages 32 and 33. While the building appears severely damaged, the building structure was mostly intact. Only a small portion of the roof deck had been blown off.
The checklist that our team used includes a place for the building name, number, date, and a crude building plan sketch (with north arrow) to further describe the location and extent of the damage. Also, there is a place to make a recommendation as to whether to repair or replace a building. In some cases, IEI engineers had to determine whether the damage was pre-existing or not.Typically, the presence of rust or discoloration helped to identify preexisting damage.
Each team was responsible for a particular area of the complex. The teams worked building by building completing the check list, taking notes and photographing the damage. The paperwork was completed, including the floor plan sketch, before proceeding to the next building.
Observed damage – The building types observed included those constructed of precast concrete, concrete masonry (both reinforced and unreinforced), structural steel, light gauge metal, wood, and metal buildings. They varied from single story to mid-rise buildings. This project was unique because the facility is remote from adjacent structures in the community, and there is only one building owner. Therefore, all of the buildings affected by this wind event were accessible to the team. The engineering teams were able to see first hand how various building types performed during the tornado, as well as how the performance – or lack of performance – of specific building types affected adjacent structures.
Generally, the precast buildings performed the best, followed by the structural steel and metal buildings, and lastly the concrete masonry and wood buildings. The single-story precast structures are long, narrow buildings that serve as pit garages. The only damage observed at these buildings was to some of the exterior signage and ballasted roofs.
With the exception of damage caused by the disintegration of adjacent masonry buildings, the structural steel buildings performed very well. For example, the Weaver Skybox building’s structural steel frame was intact with little damage.
Similarly, the metal buildings also performed well. The fact that the metal building industry uses a less restrictive deflection criteria than that typically used for structural steel buildings was evidenced by the extent of damage to the interior finishes, particularly at the lay in ceilings.
The primary damage to the masonry buildings resulted from uplift forces as the structural steel was lifted off its support at the top of the walls. This occurred in both the unreinforced masonry (URM) buildings, as well as those recently constructed of reinforced masonry. At the URM buildings, the top layers of concrete masonry units (CMU) simply failed in tension at the horizontal mortar bed. Unfortunately, the steel that was blown from the roof structure of the URM buildings became projectiles and caused much additional damage. In addition to causing minor damage to the infield buildings, one of these beams knocked over a light pole adjacent to the track then knocked over two tractor trailers into an adjacent metal building pit garage. Another beam traveled into an infield URM concession building with a concrete roof and knocked out a load bearing wall, causing half of the building to collapse. Conversely, the URM buildings that had concrete observation roof decks apparently resisted the uplift wind pressures.
There were two identical, single-story CMU structures in the infield that housed concessions, restrooms, and shower facilities. These buildings appeared to be newly constructed of reinforced masonry. One of the two buildings lost a portion of its bar joist and metal deck roof. Evidenced by some of the joist embedment plates that had been pulled out of the top of the masonry wall, adequate anchorage was never achieved during design or construction. The hooked rebar that was welded to the bottom of the embedment plate was not long enough to be developed into the masonry wall. The joist and deck that were blown off became projectiles as well.
The conclusion drawn from our observations is that the continuous load path from roof to foundation is more consistent in structural steel and metal buildings as compared with masonry buildings. The quality of both steel building types can be controlled more easily both in the shop and in the field. And while masonry gives the comfort of a solid and heavy structural material, the consistency of its load path is dependent on the detailing and ultimately the skill of the mason and the level of inspection in the field.
Reporting
IEI engineers conducted a cursory walk through on Friday afternoon and by the end of that weekend mobilized multiple two-person crews and assessed 18 buildings.
By the following Wednesday – just six days after receiving the call to assist with the project – IEI completed assessments of the 41 buildings and the draft report, which included write-ups and photographs for each building. As time was of the essence on this project, the draft report, completed checklists, and photographs were posted to a confidential website for immediate review by the owner and contractor.
Legal aspects
The risks of conducting structural condition assessments often exceed the anticipated profit. Therefore, it is important to manage these risks throughout the entire project – from proposal preparation to report completion. Also, anyone performing condition assessments should verify that their organization is fully insured for this potentially hazardous work. Structural Condition Assessment by Robert T. Ratay provides good information about controlling your risk.
Conclusion
Not only did AMS meet its deadline for making the necessary repairs to the facility prior to the Bass Pro Shops MBNA 500 in October, but it made significant improvements to the raceway complex. IEI is proud to have played such a key part in the recovery from this disaster. This project served as an invaluable learning experience for the company’s seasoned engineers and interns. It allowed the structural engineers to hone their skills in identifying signs of distress and the probable causes for it. The experience will assist IEI’s engineers in performing future design work, as well as other facility condition assessments, for both private and public clients.
Scott L.Weiland, P.E., is the president of Innovative Engineering Inc., a structural engineering firm based in Atlanta. He has more than 25 years experience in both the design and construction industries.
Evaluation Team
Project Name
Atlanta Motor Speedway
Owner
Speedway Motorsports, Inc., Concord, N.C.
Structural Engineer
Innovative Engineering Inc., Atlanta
Consulting Engineer
Savant Engineering, LLC, Atlanta
Structural condition assessments of 41 buildings at the Atlanta Motor Speedway facility, such as at the Champions skybox below, were required to be performed before rebuilding efforts could begin.
Download a PDF version: Atlanta Motor Speedway - Assessing the Damage
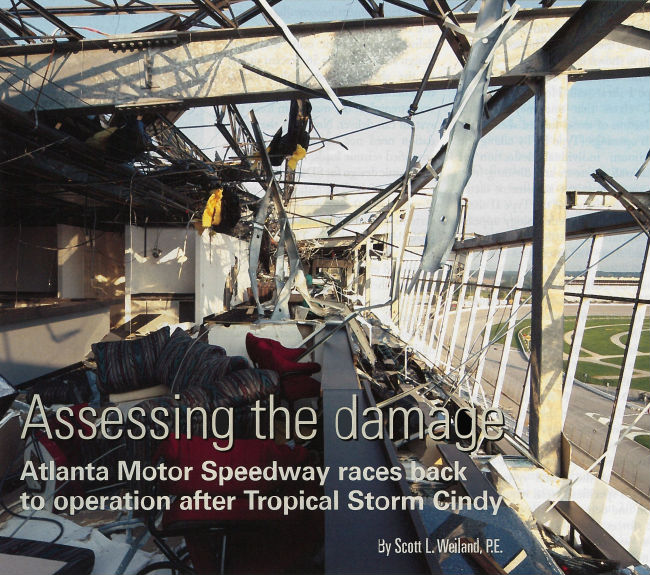
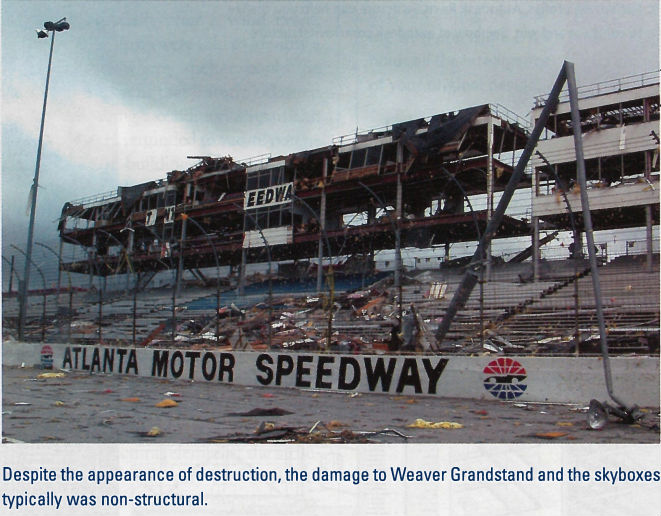

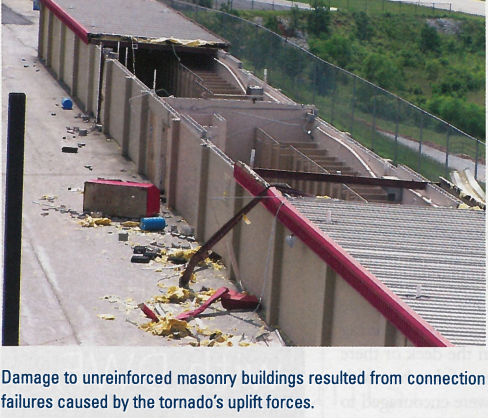
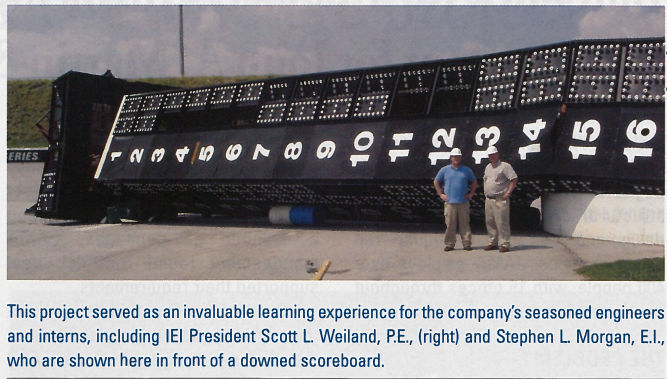